
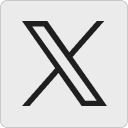




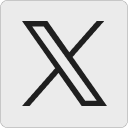



Your business tools, equipment and machinery can be key determining factors for the success or failure of your enterprise. Consider investing in innovative technology to help your business expand if you are experiencing increased machinery downtimes and productivity losses. The correct equipment may help you enhance your operations, productivity, innovation capability, and bottom line. It is best to have an investment strategy to cover your short and long-term needs to benefit from this large capital investment. You will find the tips below useful.
- Understand your financial capacity
Having financial constraints in business is not always a bad thing. Rather it encourages budgeting and effective money management. For example, you may not be able to purchase the best equipment right now, without jeopardizing other business processes that also require funding. An experienced finance manager can advise you on how much you have available to spend at any point in time. There is also the option of requesting help from financial organizations such as banks. With this assistance, it is critical to verify that the equipment will generate enough revenue to allow you to pay back within the time frame specified. Knowing your financial boundaries serves as the foundation for developing a budget.
- Lease or buy?
Everybody would prefer a new machine over a used one. However, the latter may be the most cost-effective solution at the moment. You will have to exercise great precautions when buying a used piece of used machinery. Check to see if there is a conflict of interest about it or if it has been stolen. Leasing may be the best alternative if purchasing does not provide you with good value. It is also the best option if you want to get equipment that lasts long. You don’t want to get equipment that will only last a year or two before you have to buy another similar one.
- Get an outside opinion
Depending on the investment size, engaging with an external consultant who can help you analyze your needs and ensure you get the most out of your purchase may be worthwhile. Initially, you may consider critical criteria such as capacity, present resources, and staff utilization. The most typical method is to perform a cost-benefit analysis to weigh the advantages and disadvantages to justify your decision. Whether you are shopping for new or secondhand machinery to operate your business, you should look into it before you buy. You can hire a third-party specialist to evaluate and test the equipment you’re thinking about buying. You can also consult the equipment manual or online resources to guarantee the equipment is a solid fit for your business. For instance, the Caterpillar manuals can provide more information about your large construction and industrial machine.
- Shop around for suppliers
Industrial machinery varies in price. Their prices might vary depending on various factors, such as the complexity and new features, production material quality, manufacturer or brand, and so on. Avoid choosing the cheapest option when shopping because it appears to be the most practical. Instead, probe deeper to unravel the reason behind the pricing. This doesn’t also suggest that the high pricing is a guarantee of superior quality. When comparing pricing, consider various criteria, including ratings and market feedback, to make a more informed buying decision.
- Consider training needs
Too frequently, business owners fail to consider the time, money, and resources needed to educate personnel on new equipment. Your staff may take a while before adjusting to the new machine or processes, which can tax your production. You can plan for your employees’ learning curve when you bring in a new machine, perhaps with new functionalities. Before you bring in any machine, consider if you have the funding to deal with potential downtimes during the adjustment period. Make time to train your personnel while ensuring your business operates at full capacity.
- Keep your choices green
Energy efficiency should be at the forefront of all your machine purchase decisions. You will save money and contribute to making the world safer and healthier. Also, keep your employee’s health in mind when purchasing equipment. This includes avoiding machines that release hazardous fumes while running. The poisonous gases may not have an immediate effect. However, constant exposure and inhalation can be harmful in the long run. It would be best if you researched the environmental effect of your new equipment and how you can dispose of your old equipment in a way that minimizes its environmental impact.
Aside from the significant upfront cost of purchasing the machine for your business, maintenance and potential replacement costs can be costlier if you invest in the wrong machines. The tips mentioned above can be useful for guiding your machine buying decisions.

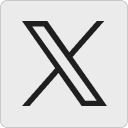




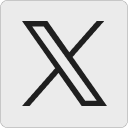



Leave a Reply